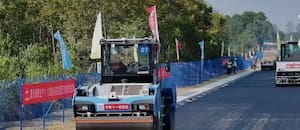
Proyecto Ñandú: prótesis deportivas diseñadas en La Plata
Las personas que han padecido una amputación en sus miembros inferiores y quieren practicar un deporte suelen encontrarse con una importante limitación que va más allá de su condición: la económica. Las prótesis de competición no solo son más caras que las de uso cotidiano, sino que además no se fabrican en el país. Esto tiene como consecuencia que la persona termine usando una prótesis común y se arriesgue a sufrir una lesión o que, directamente, abandone la actividad.
Ingenieros aeronáuticos de la Facultad de Ingeniería de la Universidad Nacional de La Plata (UNLP) trabajan desde hace algunos años en el Proyecto Ñandú, que consiste en el diseño y fabricación de una prótesis transtibial de competición. Según los cálculos preliminares, el costo de la materia prima y los insumos necesarios para fabricarla va de 200 a 400 dólares, mientras que las prótesis importadas rondan los 18.000 dólares. Por lo tanto, la prótesis fabricada por los ingenieros locales sería, sin contar la mano de obra, hasta 90 veces más económica.
"Queremos generar prótesis de competición que sean iguales a las importadas pero fabricadas en el país, ya que hoy en día no las hay. Para esto, lo más importante a tener en cuenta es la comodidad del usuario y la capacidad de soportar las cargas de competencia, que son muy altas", contó a TSS Álvaro Benítez Franco, integrante de un equipo que se completa con Lucas Sznajderman (director), Juan Ignacio Villar (codirector) y Marco Fontana.
Las prótesis del Proyecto Ñandú están orientadas al atletismo, específicamente a las carreras de 100, 200 y 400 metros. Los destinatarios principales son atletas con amputaciones de miembros inferiores y niños, niñas y adolescentes que quieran iniciarse en el atletismo. En las competencias de alto nivel, no hay reglamentaciones que limiten las prótesis en conceptos dinámicos o mecánicos pero sí geométricos, lo que implica que no está permitido darle al atleta una altura mayor o tener partes motoras que mejoren el rendimiento.
Uno de los principales desafíos para el equipo es el hecho de que las prótesis son, de por sí, objetos muy personales dado que cada persona posee características diferentes en altura, peso, zancada y fuerza transmitida al piso. Todas estas variables son relevantes a la hora de desarrollar la pieza (parte curva que hace las veces de pie). Por eso, el objetivo es lograr un modelo genérico que pueda adaptarse a cualquier atleta con las mínimas modificaciones posibles.
En cuanto a los materiales, Benítez Franco dice que "la pieza está construida con materiales compuestos, por una cuestión de resistencia y de peso. Nosotros la estamos desarrollando en fibra de carbono (obligatoria para competidores) y fibra de vidrio, que es más barata". La bota, en tanto, que es la parte sobre la que descansa el miembro amputado del atleta, es fabricada por un ortopedista, mientras que el anclaje que une la bota con la pieza puede realizarse en polímeros de impresión 3D o en metal.
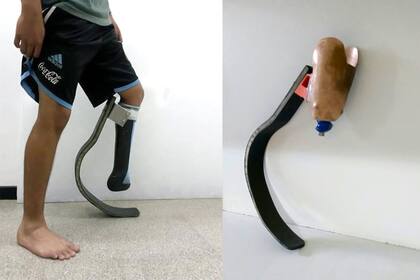
Para diseñar, fabricar y probar los modelos, los investigadores se valieron de tres procesos. En primer lugar, la revisión de estudios internacionales para explorar qué propiedades mecánicas debe tener la pieza. En segundo lugar, la colaboración de un atleta y su experiencia en la utilización de prótesis de competición. Por último, cuentan con una plataforma para la realización de ensayos de caracterización y evaluación de los parámetros biomecánicos del usuario, como el estudio de la marcha y de la carrera, entre otros factores.
"Ahora estamos en una etapa de revalidación para mejorar la pieza, especialmente en lo que respecta a la rigidez. Entre otras cuestiones, el atleta que colabora con nosotros nos dijo que el modelo al que llegamos estaba bien para caminar, pero que en situaciones de carrera se sentía un poco blanda. Por eso, seguiremos realizando ensayos hasta dar con el modelo que necesitamos", indica el investigador. Una dificultad que tuvieron hasta el momento en la elaboración de la prótesis es el hecho de que la mayor parte de los materiales es importada, aunque aún así la disminución de los costos es sustancial.
Otra dificultad es el tema económico, ya que el proyecto está realizado sin fines de lucro. "Es a pulmón, no cobramos ni ganamos dinero, por lo que solo podemos dedicarle nuestro tiempo libre. Por suerte, la universidad nos avala a través de un proyecto de extensión y nos otorga un dinero con el que podemos comprar algunos materiales", dice Benítez Franco. Una vez que logren llegar a una prótesis factible de reproducir y adaptar a cada caso, el tiempo de diseño y construcción de la misma llevaría menos de una semana.
"La idea es terminar el modelo a fin de año o mitad del que viene, para así empezar a producir. Lo que queremos es devolverle a la sociedad un poco de lo que nos dio a nosotros. Lo ideal sería conseguir que el Estado financie la fabricación de las prótesis, ya que con muy poco podemos proveer, primero, a los jóvenes que representan al país en competencias internacionales y, luego, a cualquiera que quiera iniciarse en el deporte", dice el investigador.
- 1
- 2
Las 5 señales que muestran que tenés una mentalidad positiva, según un análisis de IA
- 3
Fin del impuesto PAIS: del iPhone 16 al Galaxy S24 Ultra o la PlayStation 5, cómo cambia su precio para traerlos al país desde enero de 2025
- 4
¿El número mágico? El porcentaje de batería para cargar el celular y que dure más