Impresas en 3D: así son las zapatillas del futuro que se fabrican a medida

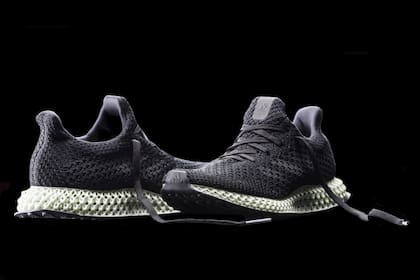
Aunque la industria del calzado deportivo parece estar por momentos más enfocada en la moda que en el deporte (una tendencia inaugurada y promovida por las propias marcas, claro), todavía surgen chispazos de innovación que invitan a imaginar un futuro cada vez más presente. A lo largo de su variada historia, las zapatillas impulsaron el uso cotidiano de ciertas tecnologías. Algunas de ellas fueron exclusivas de otras áreas -la primera cámara de aire fue una creación del ingeniero aeronáutico Frank Rudy, luego adoptada por Nike- y otras estuvieron más ligadas a la ciencia ficción, como las zapatillas autoajustables con las que Marty McFly se sorprendía en la segunda parte de Volver al Futuro. Y así como el nylon y el velcro constituyeron grandes avances en su momento, hoy todo lo que puede considerarse novedoso pasa por la impresión 3D .
El pasado 18 de enero en Nueva York, Adidas presentó y puso a la venta la Futurecraft 4D, una zapatilla de running de alto rendimiento, con entresuelas fabricadas con impresoras 3D. Pero diferencia de otras presentaciones, buena parte de la novedad pasaba por la venta y no por no ser la simple presentación de un prototipo. El calzado era una realidad, no una promesa a futuro. Cualquiera con 300 dólares y algo de suerte -sólo fueron lanzados cinco mil pares en unas pocas tiendas- podía presumir de sus zapatillas, sea o no runner. La entresuela de la Futurecraft 4D está fabricada con la tecnología Digital Light Synthesis -propiedad de Carbon, una compañía situada en Silicon Valley- y es, básicamente, una sola pieza moldeada a partir de líquido, que se convierte en sólido gracias a la luz y el oxígeno.
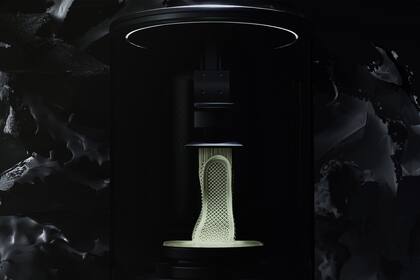
El diseño de la Futurecraft 4D se apoya en toda la información recogida por la marca alemana durante años de estudio de la pisada de los atletas, lo que permitió confeccionar una entresuela con distintos tipos y niveles de amortiguación, según la parte del pie que la utilice. El talón está diseñado para absorber el impacto, la parte media facilita la transición del talón a la punta del pie, y la punta está diseñada para el despegue. Y ese es justamente otro de los objetivos del calzado: además de la amortiguación, ofrece lo que se denomina “retorno de energía”, el término técnico y marketinero que explica lo que en el barrio se llamaría rebote. Cada uno de los 20 mil puntos independientes que se extienden por toda la suela cumplen con estas funciones.
Del mismo modo en el que las capelladas tejidas de una sola pieza (Flyknit o Primeknit, por ejemplo) se fueron convirtiendo en el estándar para el calzado deportivo, la impresión 3D busca ser la próxima solución en la customización de las zapatillas. Con un estudio de pisada y el conocimiento de la morfología del pie, será posible producir un calzado personalizado, diseñado en su totalidad para un determinado pie. “La idea de escanear tus pies e imprimir una suela 100% customizada de acuerdo a tu forma, tu pisada, tu peso y la actividad que vas a hacer no es lejana en el tiempo”, dice Jared Goldman, director senior de Diseño de New Balance, marca que viene incursionando -aunque todavía a una escala menor- en la impresión 3D. “Será el próximo gran cambio en la industria del calzado en los próximos 5 a 10 años”, agrega. En 2016, en ocasión de la Maratón de Boston, New Balance lanzó un calzado diseñado y fabricado en su planta de Lawrence, realizado con impresión 3D. La Zante Generate tuvo un precio de 400 dólares, pero sólo fueron fabricados 44 pares.
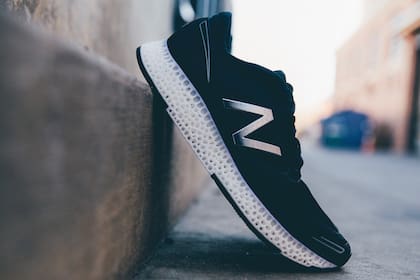
Mientras que las entresuelas fabricadas con espumas (Boost, Lunarlon, FreshFoam) tienden a aplastarse y perder algo de forma con el tiempo, todo indica que las moldeadas en 3D solucionan ese problema. Las otras grandes contras del típico proceso de impresión 3D -el tiempo y el precio, al menos para fabricar un producto en una cantidad suficiente para poder ser comercializado- fueron solucionados con la tecnología de Carbon: la Futurecraft 4D no lleva más de una hora de fabricación.
Si bien la primera tanda fue de sólo cinco mil pares, el objetivo de Adidas es fabricar cien mil durante 2018, y aumentar esa cantidad de manera progresiva. Los 300 dólares de costo (contra los 180 de unas Ultraboost o los 190 de unas Nike Vapormax) no parecen exagerados, sobre todo si se tiene en cuenta que se trata de la primera edición de un producto que promete cambiar la industria del calzado deportivo tal como se la conoce. Basta de prototipos, es hora de producir.