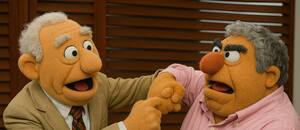
Gabriel Ortiz, de Pixart: de no tener plata para la nafta a inaugurar la primera fábrica automatizada de América latina
Gabriel Ortiz es cofundador y CEO de la empresa argentina Pixart, una planta de producción inteligente que se inauguró en Escobar y es única en su tipo en América Latina. Recorrimos esta smart factory, que se destaca por su proceso de automatización y apuesta a expandir su producción de computadoras y ampliar el desarrollo de robots
7 minutos de lectura'

De 0 a 1.000.000 en un abrir y cerrar de ojos. O casi. Pixart es una empresa argentina que lleva 25 años en la industria y acaba de inaugurar una planta inteligente en Escobar, que implicó una inversión de 8 millones de dólares.
Se trata de una fábrica -ideada para producir computadoras y robots en serie- y es un ejemplo del concepto de industria 4.0, por el nivel de automatización que propone. Es única en su tipo en América Latina, según se destacó durante la inauguración.
Los principales creadores de esta moderna unidad de producción son Gabriel Ortiz, CEO y cofundador, junto con su esposa Mariela Sanchez Otranto, de Pixart. “Ella se encargó de todo el diseño de la fábrica”, cuenta Ortiz en diálogo con LA NACION, mientras muestra algunas fotos de la obra y de los arreglos que tuvieron que encarar cuando el proyecto quedó demorado por un incendio.
Una batería, un cortocircuito y un fuego que se salió de control hace apenas 8 meses derrumbaron lo construido, pero no frenaron el sueño. “Hubo que arrancar otra vez, ¿qué se iba a hacer?”, dice Gabriel, mientras muestra en el celular otra foto de él y Mariela equipados con herramientas de trabajo, en las ruinas que hoy se convirtieron en esta smart factory.
Gabriel es un remador nato. Así lo deja ver cuando cuenta las vicisitudes que han tenido que atravesar en estos 25 años que llevan en el mercado. En sus inicios la empresa ofrecía soluciones integrales basadas en Linux, con la adaptación requerida por los clientes. Con el tiempo se embarcó también en el desarrollo de hardware para diferentes organizaciones.
Vendieron equipos en numerosos lugares, con foco en proyectos educativos como es el caso de Conectar Igualdad, por medio de acuerdos con los Ministerios de Educación de las provincias de Corrientes, San Luis, La Rioja y Córdoba. También comercializaron soluciones propias de antirrobo y de Administración de Dispositivos Móviles (MDM) en Latinoamérica.
Sin embargo, todo esto no ocurrió de la noche a la mañana. Al comienzo no fue fácil. “Recuerdo una vez que no tenía ni para pagar la nafta del auto. Con lo poco que me quedaba en el bolsillo apenas me alcanzó para tomarme el 60″, cuenta Gabriel.
También recuerda una oportunidad en que tuvo que recibir a un cliente y apenas le alcanzó dinero para agasajarlo con una pizza. “Me preguntó si tenía gaseosa y le dije que había salido a comprar, pero que no había encontrado nada porque estaba todo cerrado; pero la verdad era que no me había alcanzado para nada más”, comparte, entre risas.
Cuando fue a buscar el primer pago tras concretar una venta importante, le entregaron un abultado cheque que lo emocionó. “Yo esperaba recibir algo en efectivo porque no tenía un peso”, recuerda. Y gesticulando, recrea la sorpresa que sintió cuando vio la cifra en ese primer cheque: “eran muchos ceros juntos. No estaba acostumbrado”, confiesa.
Una fábrica de PC y robots
De aquellos inicios a inaugurar una fábrica 4.0 transcurrieron más de dos décadas en las que no hubo tiempo de aburrirse. En los 4500 metros cuadrados que conforman esta moderna unidad de producción hay brazos robóticos, equipos de testeos automatizados y paneles de control de última generación.
“El trabajo pesado lo hacen los robots, y las configuraciones técnicas quedan en manos de programadores e ingenieros”, cuenta Ortiz. El 90% del proceso de producción está automatizado. Hay equipamiento proveniente de diferentes polos tecnológicos en el mundo, como Japón, China y Estados Unidos. Además, emplean insumos locales y de otras latitudes. Los humanos -cerca de 40, entre programadores e ingenieros- se encargan de tareas estratégicas como ser el diseño, programación y control de este equipamiento.
Con esta nueva fábrica, que tiene dos plantas, se planea aumentar la producción de portátiles y apostar al desarrollo de robots. Durante la visita se pudo ver un prototipo, bautizado Eva, que está pensado para realizar atención al cliente en diferentes entornos, como aeropuertos. Este tipo de robots, que surgen de equipos importados y modificados en la planta de Escobar, se harán en serie para ser comercializados en diferentes partes del mundo.
Además de tener una consolidada presencia en el país y Latinoamérica, Pixart planea desembarcar en Estados Unidos. “Toda la fábrica está alimentada con paneles solares. Se producen 270 kw de energía solar. Somos autosustentables”, remarca Gabriel, para dejar en claro el compromiso de la compañía con la utilización de energía limpia. “Esto es muy importante para reducir la huella de carbono que, además, es un requisito para exportar. Además, estamos muy cerca del puerto, así que los camiones recorren pocos kilómetros”, subraya.
Esta flamante plata, que se comenzó a idear en 2019, implicó una inversión de 8 millones de dólares, según dicen desde la compañía. Cuando vino la pandemia, lejos de echarse atrás con este proyecto, Gabriel interpretó el contexto de alta demanda de equipos y escasez global de chips como una oportunidad para apostar con más fuerza a la producción nacional. “Había que encontrar una solución porque con las limitaciones por el Covid y los cierres de fábricas no alcanzaba, ni alcanza, con lo que se está produciendo en el mundo”, reflexiona.
Durante el recorrido que hizo LA NACION por las instalaciones, se pudieron ver las diferentes estaciones que conforman esta smart factory. Hay máquinas capaces de colocar unos 800 mil componentes por hora y brazos robóticos que pueden ser configurados para realizar varias tareas, como las de ajustar tornillos, empacar componentes en caja o trasladar productos.
Cada estación de fabricación envía información que está centralizada en el panel de control para así optimizar el proceso de fabricación. A su vez, todo el equipo tiene acceso remoto con el software de Pixart para asegurar la información y tomar medidas de seguridad. En este proceso de innovación tecnológica, la empresa contó con el apoyo de programas de financiamiento del Ministerio de Economía de la Nación.
Otro punto interesante son las máquinas que se emplean para la inspección de los productos. Son grandes cajas de metal que en su interior cuentan con cámaras inteligentes Real Sense de Intel, así como pequeños CPU. Así se puede hacer el monitoreo de los diferentes componentes de las computadoras ensambladas en la planta. Todo el procedimiento queda grabado y funciona como una manera de garantizar la calidad de la inspección realizada. También hay otras tecnologías automatizadas de inspección de pasta de soldadura y ópticas.
“Además de las cámaras Real Sense, les proveemos de procesadores que se encuentran también en los insumos empleados para hacer las computadoras. Estamos orgullosos de acompañar a Pixart en el desarrollo de esta fábrica con tecnología de punta. Es un claro ejemplo de que la transformación digital se encuentra en todos lados. En este caso, en la industria que ahora podemos llamar 4.0″, dijo Adrián de Grazia, Argentina country lead & Americas Digital director de Intel, durante la inauguración de la planta.
Pixart también cuenta con un tablero inteligente que permite optimizar el proceso de fabricación. Con este equipamiento se pueden identificar cuellos de botella, equilibrar las cargas de trabajo y reducir los tiempos de suministro. Una de las principales funciones es hacer un análisis estadístico del proceso para poder realizar un mantenimiento preventivo, predictivo y prescriptivo de los equipos, así como crear informes a los proveedores sobre piezas defectuosas.
“Se reemplazan las tareas mecánicas por la automatización -aclara Ortiz-. Se quita el trabajo pesado y se busca emplear personas para el desarrollo de otras tareas”.
Últimas Noticias
Ahora para comentar debés tener Acceso Digital.
Iniciar sesión o suscribite