
Reciclado de neumáticos: cómo funciona la planta que reduce el caucho a pequeñas partículas

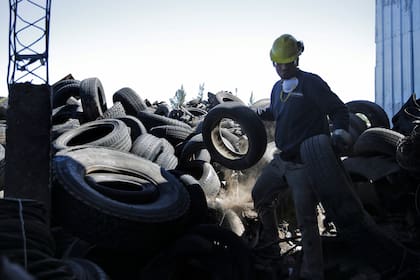
Un neumático de camión tiene un peso aproximado de 50 kilos y es lo suficientemente incomodo para ser manipulado por una persona. Pero cuando está montado en la máquina destalonadora, entregado a una barra de hierro que avanza hacia el corazón del caucho, se vuelve vulnerable. Aún más cuando el gancho ubicado en la punta le arranca las telas y los filamentos de acero, los otros componentes de la cubierta. Es el primer paso de la descomposición de un elemento que, al final del proceso, quedará reducido a partículas de cinco milímetros de diámetro, una de las mejores formas de reciclarlo, para ser reutilizado, por ejemplo, en canchas de fútbol sintético.
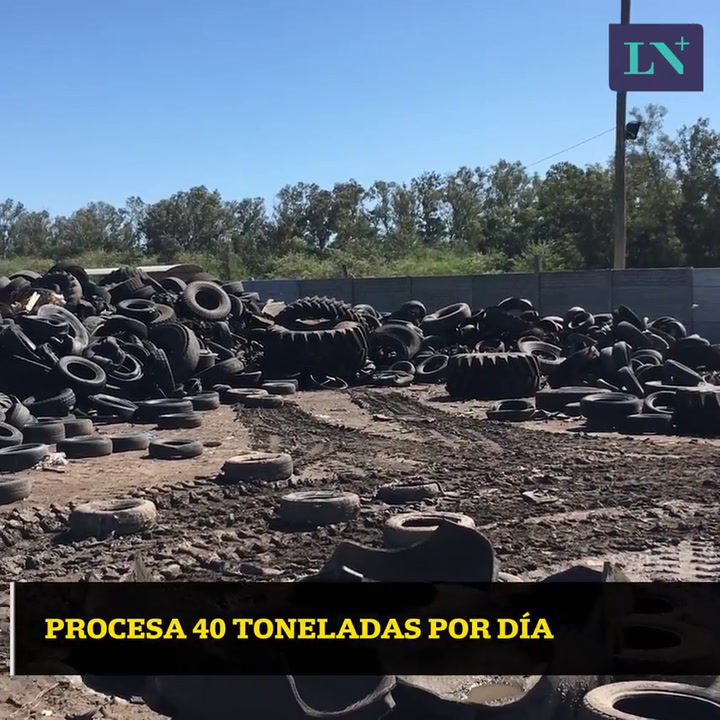
La actividad transcurre en la planta industrial ubicada a un costado del Camino del Buen Ayre, a pocos metros del ingreso del complejo Norte III de la Coordinación Ecológica Area Metropolitana Sociedad del Estado (Ceamse), donde llegan toneladas de cubiertas de toda el área metropolitana, principalmente de la ciudad de Buenos Aires, y de otras provincias. Allí se inicia el camino final de los neumáticos que ya no sirven, los descartados en las gomerías y en las fábricas.
A falta de políticas que establezcan un cronograma de reducción del caucho, que puede tardar hasta 600 años en degradarse en tierra, las plantas de reciclado aparecen como una alternativa. Las unidades que no ingresan a este proceso terminan en los techos de las gomerías, en campos o en baldíos transformados en basurales. Se convierten en focos de contaminación y peligro para la salud.
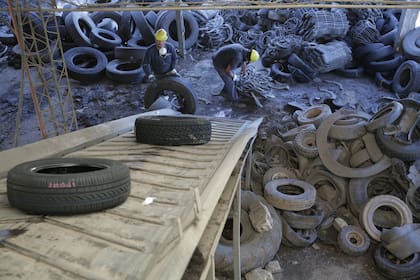
En la ciudad de Buenos Aires y el área metropolitana los neumáticos en desuso suman unas 65.000 toneladas por año, la mitad de lo que se genera en todo el país. Solo el 20% se recicla en la planta Regomax, que funciona desde 2010 mediante un convenio con el Ceamse. Es una de las pocas instalaciones donde el reciclado se realiza en forma industrial y el producto, un caucho granulado, se utiliza en las canchas de fútbol sintético de clubes de diferentes categorías o de alquiler privado.
"Tenemos capacidad para procesar entre 50 y 60 toneladas diarias. Mensualmente recibimos unas 800 toneladas, aunque tenemos posibilidad de tratar hasta 1400 toneladas por mes. Trabajamos en tres turnos diarios, cinco días a la semana, y aún estamos con capacidad ociosa", resume Daniel Rodríguez, gerente de Regomax, mientras camina por las distintas zonas de la planta: acopio, trituración, selección, separación de acero y textiles, granulado y empaquetado, en bolsas de 30 y 50 kilos. Las máquinas trabajan a todo ritmo. El ruido hace inútil las palabras porque no se escucha ni hablando cerca del oído de otra persona. Hay que usar protección auditiva (además de lentes, cascos y otros elementos de seguridad) para reducir el impacto sonoro.
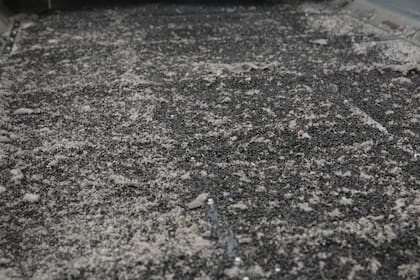
Los neumáticos que no son de camiones no necesitan pasar por la destalonadora y, en el inicio del viaje final, van directamente a una trituradora a través de una cinta transportadora. En esa etapa se reducen a trozos de entre cinco y diez centímetros y luego avanzan hacia la siguiente instancia de granulado y separación. Mediante un sistema de imanes el 95% del acero se desprende y el caucho y la tela pasan a una nueva estación.
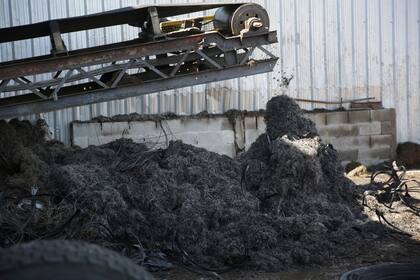
"En cada una de las cuatro etapas de granulado se separa el nylon y el acero que va quedando. En el producto final, con partículas de entre dos y cinco centímetros, no debería quedar nada de acero. La tela se separa por aspiración y es el único residuo que se genera porque el acero se funde y el caucho se utiliza en canchas de fútbol. También se lo puede usar en la construcción o en piezas moldeadas", cuenta Rodríguez.
Permisos y autorizaciones
En la ciudad no existe una política de reducción progresiva de cubiertas que ya no se utilizan. "Fomentamos que tanto las empresas de recolección de residuos como los recuperadores ambientales que recorren la ciudad acerquen los neumáticos fuera de uso a los puntos verdes o el Centro de Transferencia", explicó Eduardo Macchiavelli, ministro de Ambiente y Espacio Público de la ciudad.
En la Ceamse, en cambio, se generó un sistema de permisos y autorizaciones para empresas y municipios mediante el cual quedan exentos de pagar la tarifa correspondiente por el tratamiento en el predio de disposición final de residuos industriales no peligrosos. El costo que se evitan es de $2475 por tonelada, con transporte y transferencia, o $1300 si el material fuera directamente a relleno. También, para incentivar el envío, se otorga una tarjeta de neumático de uso limpio.
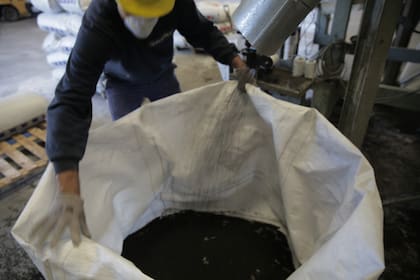
"Las gomerías, los fabricantes de neumáticos, las empresas de transporte -que son los grandes generadores de neumáticos en desuso- tienen que transportar la carga hasta el complejo Norte III. Ese es el único gasto que afrontan", explicó el ingeniero Marcelo Rosso, gerente de Nuevas Tecnologías y Control Ambiental de la Ceamse. "En otros países, como Uruguay, Chile y Brasil, existe la figura de ‘responsabilidad extendida’ al productor que debe hacerse cargo de la logística y el tratamiento", agregó.
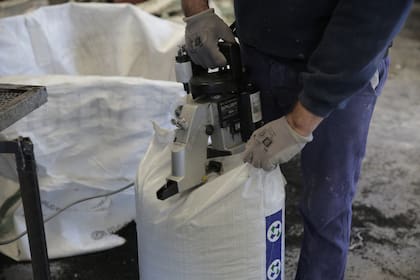
El 70% de los neumáticos que no llegan a las plantas de reciclado, que existen en distintas ciudades del país aunque con una escala de producción menor, terminan -como se dijo- en rellenos sanitarios, en los techos de las gomerías, en basurales a cielo abierto o al costado de las rutas. No es contaminante material, pero su potencialidad de daño es elevada por las enfermedades que puede generar. Una regulación sobre su disposición final sería el comienzo de la solución.
- 1
- 2
La tendencia que se instaló en la costa atlántica después de la pandemia y cada año se afianza más
- 3
Menopausia: el impacto poco admitido, pero que afecta a 7 de cada 10 mujeres, y consejos para atravesar mejor esta etapa
- 4
“Cada planta tiene nombre y apellido”: un frustrado viaje de 15.000 km inspiró la apuesta de un rosarino en un pueblo mágico