Las automotrices pisan el acelerador para hacer vehículos más livianos
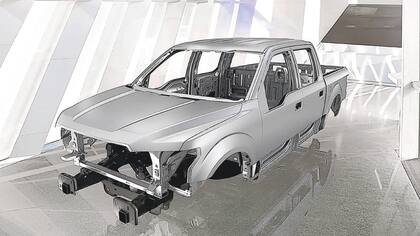
TROY, Michigan—Inclinados sobre un microscopio que aumenta los objetos 2.000 veces, dos ingenieros de un fabricante noruego de piezas especiales de aluminio analizaban uno de los componentes de riel de techo que acaban de producir artesanalmente para un nuevo cliente automotriz.
Lo que los ingenieros ven bajo el lente de su microscopio resume el futuro de la fabricación de automóviles: se trata de una parte tan fuerte como la que están reemplazando, pero que pesa menos de la mitad.
En su búsqueda de nuevas maneras de fabricar vehículos más livianos, reducir las emisiones de carbono y aumentar el ahorro de combustible, la industria automotriz global no deja molécula sin revolver.
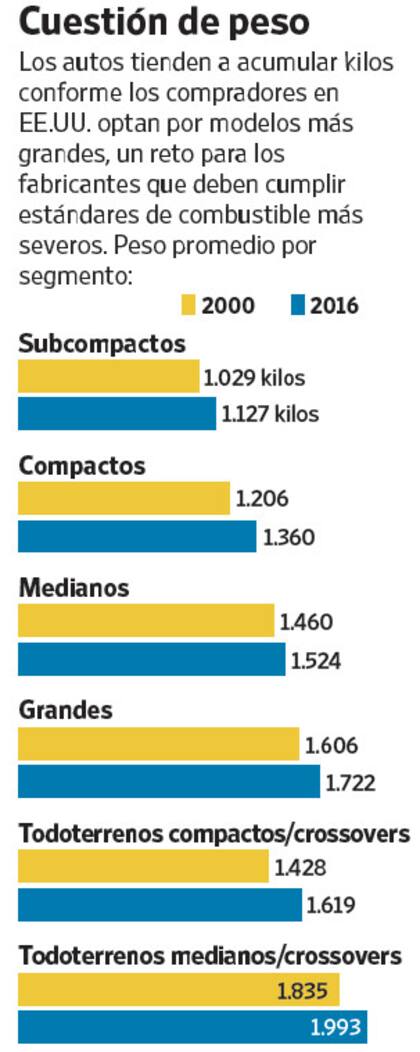
Normas más estrictas de emisiones y ahorro de combustible en Estados Unidos y otros países es-tan haciendo que los fabricantes no sólo usen más aluminio en sus autos sino que también prueben otros materiales como magnesio, aceros de alta resistencia, fibra de carbono, madera comprimida e incluso soya. Cada 10 libras (4,5 kilos) menos de peso representan entre 10 y 15 libras menos de dióxido de carbono arrojadas a la atmósfera cada año.
Pero como con cualquier dieta, perder peso no es fácil. Los nuevos materiales pueden ser costosos. Algunos son difíciles de trabajar y otros no se adaptan bien al proceso de fabricación de automóviles.
Tal vez el mayor desafío son los propios vehículos: la mayoría se han vuelto más grandes y más pesados. En los últimos 20 años, los automóviles y vehículos utilitarios deportivos que andan por las carreteras de Estados Unidos han aumentado entre 136 y 226 kilos su peso.
"El tamaño ha ido definitivamente creciendo en todos los segmentos durante al menos los últimos 10 años", dice Charles Klein, director global de estrategia para dióxido de carbono de General Motor Cgo. "Un auto compacto es ahora casi tan grande como un auto de tamaño mediano era hace 10 años. También usted está viendo mucho más contenido en un vehículo, ya sea por seguridad o por otras características, tales como una cámara trasera. Todo eso suma peso".
El típico auto compacto, que en 1996 pesaba unos 1.153 kilos, hoy pesa unos 1.360, de acuerdo con los analistas de la industria de Kelley Blue Book. Aunque hay excepciones: la todoterreno deportiva subcompacta, por ejemplo, redujo su peso. En 2011, cuando salió al mercado, pesaba 1.417 kilos; actualmente pesa en promedio 1.382 kilos.
Estas cifras, dice Klein, demuestran cuánto camino le queda por recorrer a la industria. Los fabricantes que no logren bajar de peso tendrán más dificultades para cumplir con las nuevas normas de economía de combustible que entrarán en vigor en 2025 y que requieren que los vehículos aumenten su eficiencia de combustible entre 10% y 20%.
El acero aún reina como el principal material de fabricación. Alrededor del 60% de los vehículos está construido con este material. Los fabricantes de acero también se han apurado para estar a tono con los nuevos tiempos, produciendo aleaciones más ligeras y desarrollando técnicas de calefacción y enfriamiento que reduzcan el peso del acero sin debilitarlo.
Pero las automotrices pasan más tiempo experimentando con aluminio, un material que tiene todas las ventajas del acero, pero que pesa alrededor de 40% menos. El único inconveniente es que cuesta casi el doble del acero.
Esto no ha impedido que los fabricantes conviertan partes de la carrocería, paneles de puertas, capós y techos de autos a aluminio. Ford Motor Cgo. hizo uno de los mayores intentos hace dos años cuando cambió la carrocería de su producto de mayor venta, la camioneta F-150, de acero a aluminio. El cambio le permitió bajar el peso en 317 kilos.
Sapa AS, la empresa conjunta de partes de aluminio de Orkla ASA y Hydro ASA, con sede en Oslo, abrió en Troy un centro de investigación y desarrollo para fabricar y probar autopartes para Ford, Tesla Motors Inc. y otros fabricantes. El centro de Sapa manufactura sus piezas con el denominado método de extrusión, que funciona de manera similar al juego de plastilina Play-Doh: empuja aluminio a través de unos moldes para producir una parte.
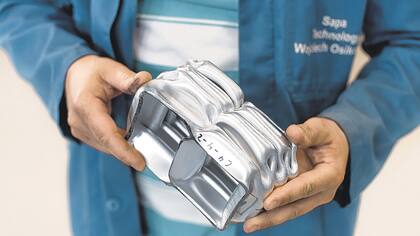
Cuando un reportero de The Wall Street Journal visitó recientemente el centro de Sapa, los ingenieros estaban inspeccionando un riel de techo de aluminio, el cual se extiende por encima de las puertas de un auto. Esta parte—por ahora experimental—pesa menos de la mitad que su equivalente de acero.
"La industria ha venido hablando acerca de usar materiales diferentes materiales durante años, y ahora ya no tiene alternativa", dice Jack Perl, vicepresidente de ventas comerciales de Sapa. "También estamos viendo un efecto dominó a medida que la industria se educa sobre los diferentes materiales".
Uno de esos nuevos materiales es el magnesio. Su aleación es 75% más ligera que el acero y 35% más ligera que el aluminio. Se calienta y vierte en un troquel para hacer una variedad de piezas. El mayor desafío del magnesio es su costo. Mientras que los precios de mercado varían, en los últimos años el magnesio ha tendido a ser más caros que el aluminio.
Para la puerta trasera de su minivan Pacifica 2017, Fiat Chrysler Automobiles NV utiliza un esqueleto de magnesio cubierto con una carcasa fina de acero. El magnesio elimina casi 10 kilos del peso de la puerta trasera. El diseño también permitió a Chrysler crear bolsillos dentro de la puerta para altavoces y luces traseras. La medida elimina la necesidad de alrededor de media docena de piezas de soporte, lo que a su vez reduce los costos.
Con el propósito de recortar costos, el fabricante francés de autopartes Faurecia SA desarrolla un proyecto de varios años para reemplazar algunas de las materias primas que utiliza para hacer fibra de carbono. En la actualidad, cada libra de fibra de carbono utilizada en la producción de automóviles cuesta US$7,30. La compañía quiere reducir ese costo aproximadamente a la mitad, US$3,60 la libra.
"Si podemos encontrar una manera de cambiar [los componentes de la fibra] para producirla mucho más barato, entonces sería algo que toda la industria podría llegar a usar", dice Christopher Aufrère, director de tecnología de Faurecia.
Alrededor del 90% de la fibra de carbono se compone depoliacrilonitrilo, o PAN, que también aumenta el costo. Faurecia está intentando sustituir ese compuesto, químico con lignina de madera o celulosa. La lignina es una sustancia orgánica que se une a las células y las fibras de una planta para formar madera. La sustancia se consigue fácilmente y es mucho más barata de producir que el PAN. Aferre espera obtener la solución para poder producir masivamente hacia 2022.
Otras noticias de Qué pasa en los negocios
- 1
Giorgia Meloni, el Papa Francisco, un gobernador peronista y un “ídolo” libertario: el podio de quienes le hicieron regalos a Javier Milei
- 2
El Gobierno oficializó la poda a la obra pública y el Tesoro le pidió a la Secretaría que devuelva 1 billón de pesos
- 3
Se vende: un fiscal detectó irregularidades en la inminente subasta de un edificio del INTA y pide evitar “posibles hechos de corrupción administrativa”
- 4
Por qué el Gobierno no salió aún del cepo y la “prueba de fuego” que deberá afrontar en 2025, según Martín Redrado