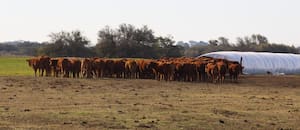
Para lograr un producto de excelente calidad se debe manejar el fuego con destreza
CONHELLO.- Hace poco menos de un siglo, zanjones repletos de leña y cubiertos con pasto y tierra ardían silencionsamente en los campos del norte argentino. Eran los antecesores de los actuales hornos de carbón, en tiempos en los que el proceso de elaboración era mucho más rudimentario. Luego, ese método fue dejado atrás por las nuevas construcciones que permitían lograr un mejor quemado y aumentar la cantidad y calidad del producto.
Así fue como numerosas baterías de hornos se levantaron en las provincias norteñas, desde las que empezaron a "bajar" hasta llegar, entre otros parajes, a La Pampa. "En el Norte es común ver campos en los que hay hasta 100 hornos, porque ahí el oficio de quemador es una tradición", explicó Rubén De Jesús, que hace 19 años construyó los hornos en Conhello y hace seis meses los reacondicionó. "Estuve diez meses y medio para parar los 30 hornos y un mes para repararlos".
Con siete metros de diámetro, una altura de idéntica extensión y fabricados íntegramente con ladrillo común, estos hornos tienen paredes de un espesor de 15 centímetros, con refuerzos triangulares de otros 15 centímetros cada tres metros. Un grosor mayor retrasaría su enfriamiento. En el centro se eleva una chimenea de medio metro de diámetro, que es de gran ayuda para manejar el fuego. "No se hace piso de material, porque no soportaría el calor", destacó Jesús, conocido como "El chaqueño".
Como un reloj
Pero ¿cómo funcionan estas "máquinas" que transforman la leña en carbón? Una vez cargados, se sellan las puertas (tienen una para la carga y otra, en el lado opuesto, para la descarga) y se empieza a prender por un hueco de unos 50 centímetros. "Después se le da unas diez horas de fuego y, una vez que éste «agarra», se tapa la abertura con barro y el horno comienza a trabajar solo."
Luego de 24 horas, el fuego comienza a bajar a las vizcacheras, 12 pequeñas aberturas ubicadas aproximadamente cada un metro y medio en la parte inferior de las paredes. Estas son indispensables para manejar el quemado. Cuando el fuego cae en la primera se la debe tapar, para que la llama se apague en ese sector y "caiga" en el siguiente. Una por una, estas bocas se van sellando en el sentido de las agujas del reloj, hasta que arde el último tronco. Es ésta la fórmula para guiar el fuego y realizar un quemado parejo. "Cuando ya ardió toda la leña, comienza a salir un humo celeste claro al principio y blanco después, entonces se tapa la boca de la chimenea para ahogar el fuego. Acá no podemos usar agua, porque se estropearía el carbón", explicó Jesús.
Todo ese proceso lleva tres días, y se deberán aguardar otros tres para que el horno se enfríe y se pueda sacar la producción. Apenas se vacíe, volverá a llenarse con leña seca y todo empezará otra vez. "No bien se saca, el carbón se carga en un camión y se despacha, para no correr el riesgo de que una lluvia lo moje."
Dos cosas preocupan a Jesús: el viento, que acelera el fuego y hace quemar mal, y la calidad de la leña, que si está "atabacada" (podrida por dentro), forma mucha ceniza y reduce el rendimiento.
La relación entre la cantidad de madera quemada y el carbón producido es otro punto esencial, que depende de la sapiencia del encargado para guiar el fuego. "Acá sacamos nueve toneladas de carbón por cada 24 de leña, que es la capacidad de cada horno. Eso es algo que se salió del libreto, porque se pronosticaba una proporción de cuatro a uno [es decir, un kilo de carbón por cada cuatro de leña] y hoy superamos el tres a uno", se enorgulleció Jesús.
Toda la producción es comprada por la metalúrgica mendocina Stein, que utiliza el carbón vegetal para elaborar ferrosilicio, un metal escencial para la fabricación de acero y que sólo se produce en seis fábricas en todo el mundo. "Allí, el carbón entero que sale de acá se coloca en grandes hornos que están continuamente encendidos y se mezcla con otros elementos. Luego se vuelca en un recipiente en el que se solidifica y se forma un bloque, que después se rompe en trozos, se embolsa y se exporta", detalló el intendente local, Luis Cervellini.
La fábrica Stein, la mayor productora de ferrosilicio de América del Sur, es el destino final de las "perlas negras" surgidas del caldenar y elaboradas en los hornos de Conhello, "herederos" de los viejos zanjones tapados con tierra y ramas que hace casi un siglo ardían en el Norte.