La planta de Toyota, en Zárate, trabaja desde enero de este año a tres turnos y fabrica una pick up Hilux cada 87 segundos; cómo se vive desde adentro producir durante todo el día sin parar
- 11 minutos de lectura'


Es un lunes soleado de julio, sin nubes en el cielo. La ciudad ya despertó con su ritmo frenético. A 100 kilómetros de Buenos Aires, en un entorno de mayor silencio, hay una fábrica de la que sale un vehículo nuevo cada menos de dos minutos, listo para probar, y que trabaja con un vértigo que contrasta con la calma de su alrededor.
Es la planta de Zárate de Toyota, la mayor fabricante y exportadora del sector y, desde el 1° de enero de 2023, la única que trabaja a tres turnos, las 24 horas del día de lunes a viernes. Del complejo de Zárate salen la pick up Hilux y el SUV SW4 para el mercado local y otros 23 países de Latinoamérica. Próximamente también producirá el utilitario Hiace, en otro formato (el modelo llegará desarmado y se ensamblará en una nueva nave dentro del predio de la automotriz, con la incorporación de algunas partes locales).

Con una jornada laboral dividida en tres turnos que suman alrededor de 6500 operarios, la fábrica hoy produce a un ritmo de una camioneta cada 87 segundos y un total de 787 por día hábil, con el objetivo de alcanzar la meta de 182.000 unidades como cifra anual. El 80% de esa producción tiene como destino la exportación. En esta dinámica intensa pero funcional, cada célula juega un rol pequeño pero fundamental. Y si hay algo en lo que la mayoría de los entrevistados coincide es que irse de Toyota una vez adentro es difícil. Algo así se siente trabajar en la planta de producción que opera sin parar.
El día en la planta
Para Enrique Smith, el día arranca a las cuatro y media de la madrugada. Desayuna mates en su casa, prepara las cosas del colegio para su hija y sale en auto para llegar a fichar, junto con otros 2000, su entrada a las 5:54 de la mañana, para que el primer turno de producción pueda empezar a las seis puntual.
A Toyota entró a los 18 y hoy ya lleva más de 10 años de trayectoria. Se desenvuelve en el área de control de calidad como team member 3A, donde su tarea es asegurarse de que la apariencia interior y exterior de cada unidad no tenga fallas. Dice que en su puesto está cómodo y no tiene planes de cambiar de lugar. “Uno viene por la plata, pero es un buen trabajo. Mientras vengas y cumplas no vas a tener drama”, señala el joven con honestidad.
Entre turno y turno hay cinco minutos de pausa y cada dos horas, recreos de 10 minutos para descansar. En los pasillos se ve gente charlando y tomando mate, como en cualquier oficina. Dependiendo del turno de cada uno, el almuerzo, o cena, es antes o después de terminar de trabajar.
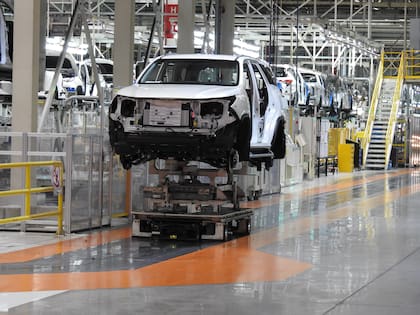
Smith es uno de los tantos chicos que entraron a Toyota con 18 o pocos más años. De hecho, su perfil es al que apuntan muchas de las búsquedas de la automotriz a la hora de reclutar personal: contar con título secundario y ganas de trabajar. Él es de Zárate, pero muchos otros viajan a diario en masterbuses a la planta ubicada sobre el kilómetro 81 de la ruta 12 desde otra localidad. Algunos desde Campana; otros, desde Luján, San Pedro, San Antonio de Areco, Gualeguaychú o Capital Federal. Dentro del predio, de hecho, existe una pequeña terminal para todos los micros que traen gente, además de la extensa playa de estacionamiento.
Cuando Toyota tomó la decisión en 2022 de empezar a producir en tres turnos desde enero de 2023 para responder a la demanda de exportación de la Hilux, parte de las obras encaradas tuvieron que ver con una ampliación del espacio de estacionamiento, para que la logística de entradas y salidas esté lo suficientemente aceitada, cuentan en la empresa.
De los 19 años a hoy
El futuro de Smith es el presente de Javier Lapalma, de 46 años, que actualmente opera como jefe del área de pintura. Entró a la planta el 18 de diciembre de 1996, a sus 19 años, cuando Toyota hacía muy poco que había llegado al país (la fábrica se empezó a construir en 1995 y la producción arrancó en 1997). “Me llegó el dato de que estaban tomando gente en una empresa japonesa. Yo había mandado mi currículum a muchos lugares y solo había tenido un trabajo de tres meses antes de empezar. Tuve que pasar por un filtro de siete entrevistas para llegar, pero elegí confiar”, recuerda hoy.
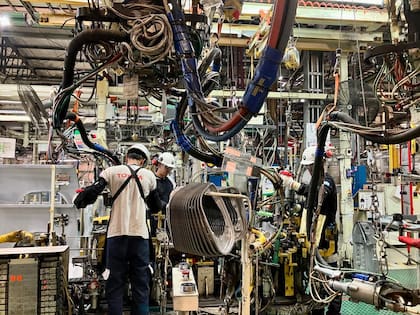
Residente de Campana, a él también le toca madrugar. Tiene una esposa con la que toma mates bien temprano antes de salir a trabajar y tres hijos con los que juega y hace deporte cuando regresa. De sus tareas, lo que más le gusta es tener gente a cargo, enseñar lo aprendido y ver cómo en Toyota se mezclan las generaciones con el paso del tiempo. “Tengo más de la mitad de lo vivido acá. La planta es parte de mi familia”, admite emocionado.
En Toyota cada operario tiene un plan de carrera y varios objetivos que les permiten escalar, según indica Diego Prado, director de Asuntos Corporativos. Entre esos objetivos anuales figuran el presentar 12 sugerencias de mejora de proceso y participar en al menos un Kaizen de calidad, también parte del Toyota Way: una actividad grupal que tiene el fin de, en un plazo de seis meses, identificar y analizar un problema y buscarle una solución.
Todas las metas son sugeridas, no obligatorias, y apuntan a aquellos que quieren progresar porque parte de la filosofía de Toyota es que “la mejora no se puede forzar”. “Es un win win. Si al empleado le va bien, la planta puede avanzar”, señala el directivo y revela que, pasado el primer año laboral, son muy pocos los empleados que eligen irse. “Todos quieren quedarse. El trato es muy bueno y los salarios -que ya son altos en el sector automotor- son aproximadamente un 30% mejores que los de una planta normal. Además, las horas extra se pagan y a los tres meses el operario empieza a cobrar premios por presentismo y desempeño laboral”, asegura, sin revelar el monto exacto.
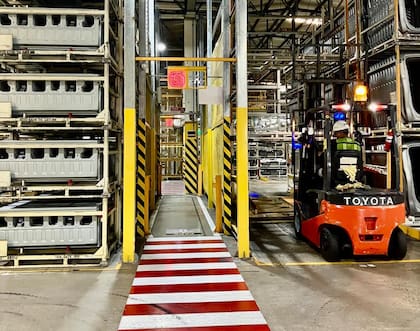
Resolver el problema a tiempo
En los pasillos de la planta abunda el orden, pero también hay vida y un extraño sentido de comunidad entre robots y personal. De a ratos se escucha una música que parece sacada de algún videoclub de Tokio durante los años en los que floreció la ciudad. Como cada elemento que forma parte del Sistema de Producción de Toyota, no es casual; es una señal sonora que se activa cada vez que un operario detecta una dificultad. A partir de este momento empieza a correr el tiempo para resolverla y, en caso de no lograrlo, cada operario tiene la autoridad para frenar la línea de producción de manera total.
Prado explica que se trata de un método efectivo porque sirve para detectar el problema en su origen sin que llegue a escalar, al mismo tiempo que empodera a los operarios. “Cada uno tiene la responsabilidad de que la pieza no pase al siguiente eslabón productivo si no está perfecta y el poder de parar todo cuando algo está mal”, explica.
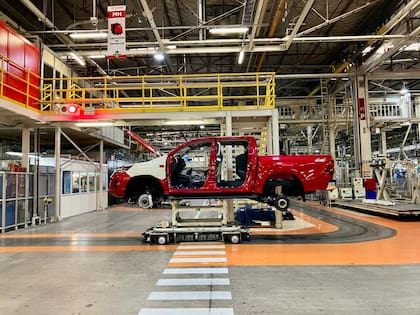
La cadena de valor automotriz es la más compleja después de la aeroespacial. Se trata de un proceso automatizado al 60% que empieza con una chapa y termina con un vehículo compuesto por más de 20.000 piezas. Hay dos tipos de robots: los segregados, que realizan una tarea de manera aislada, y los que trabajan junto con el personal.
Para Prado, lograr la misión de construir autos (y a un ritmo de funcionamiento las 24 horas) depende 100% del trabajo colectivo y no de un genio individual. “La única forma de asegurar que la Hilux que se produce en la Argentina sea igual a la que se produce en Tailandia es que las personas puedan regirse por reglas de manual. Es un acuerdo mutuo en el que cada uno asume una responsabilidad. Cuatro genios jamás podrían sacar una camioneta cada 87 segundos. Se necesita un trabajo en comunidad”, resume.
Lo justo y necesario
En línea con los beneficios que otorgan las grandes empresas que compiten por captar talento, en el complejo de Zárate hay un centro médico, un gimnasio, tres comedores y una reserva natural de 21 hectáreas que los operarios pueden visitar cuando salen de trabajar o antes de entrar. En la reserva convergen tres ecorregiones (la Pampeana, la Espinal y la del Delta e islas del Paraná) y está poblada por álamos, sauces criollos, ceibos, carpinchos, lagartos overos y más de 31 especies de aves.
En la Argentina, Toyota lidera hoy la transición hacia la electromovilidad con el 85% del total de los vehículos electrificados patentados en el país, según un informe del Siomaa. Es la única automotriz que por el momento produce híbridos en Sudamérica -los Corolla y Corolla Cross en las plantas brasileñas de Sorocaba e Indaiatuba- y, en un mercado con un promedio de 2% de ventas de vehículos electrificados, más del 8% de sus ventas hoy corresponden a vehículos híbridos.
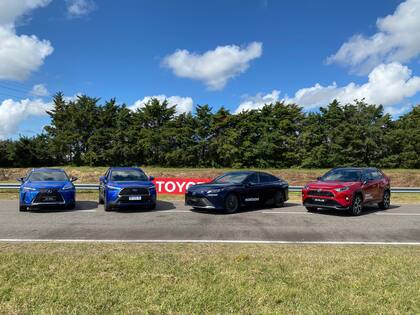
Un pilar en el que Toyota basa su sistema de producción es el principio de trabajar con lo “justo y necesario”, el legendario “just in time”, innovación nacida a fines de los años 30 del siglo XX que luego fue adoptada por otras empresas. Esto significa operar con bajo stock, para que no sobre nada. De hecho, todas las pick ups que se fabrican en la planta de Zárate ya fueron comercialmente colocadas.
Dentro de la planta, las reglas de tránsito están invertidas, y los vehículos que circulan son los que tienen la prioridad de paso. Mirar a los dos lados antes de cruzar por la senda peatonal -además de respetar religiosamente un camino señalizado para caminar- son algunas de las normas que sí o sí hay que cumplir.
Como los famosos que llegan a la alfombra roja, cada dos minutos una nueva camioneta sale por la plataforma de control de calidad, en la que personas como Smith se dedican meticulosamente a chequear que el vehículo esté listo para rodar. Una vez que esto sucede y luego de probar al azar que su mecánica no tenga fallas, la pick up o el SUV se estacionan en un playón, junto con todos los demás, donde espera a su entrega comercial o a su despacho a otro país.
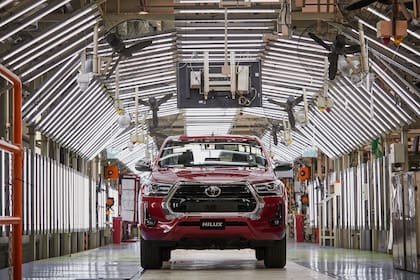
Capacitar, de noche
Antonella Acosta es analista en el área de Seguridad Industrial de la planta. Es de las que rotan sus turnos y el día posterior de la recorrida de LA NACION le tocaba quedarse a la noche, desde las 23:18 horas hasta las 5:54. Cuenta que le fascina que los operarios presten atención a sus capacitaciones, y le sorprende que esto pueda darse en un contexto de producción industrial. Por eso, siempre que puede, les busca la vuelta, con juegos y actividades que involucren pensar. “Mi éxito como profesional es que después de una jornada intensa laboral la gente me quiera escuchar”, confiesa.
Con 34 años y una trayectoria laboral anterior, dice que su sueño siempre fue entrar a Toyota en un rol relacionado con la seguridad industrial. Lo concretó a comienzos del 2022. “Siempre está el equipo a disposición para ayudarte en lo que puedas necesitar. Más que un equipo es una comunidad”, destaca con un mate en mano y sin dudar. “El enfoque humano es lo más lindo de trabajar acá. El Sistema de Producción de Toyota es una corriente empresarial que, tarde o temprano, todas las organizaciones van a tener que implementar”, agrega.
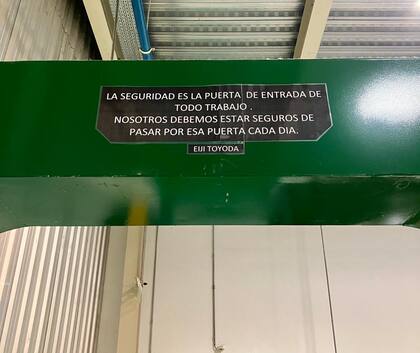
El reloj marca las seis de la tarde y el día empieza a terminar para algunos, pero la planta no para. Aunque los operarios del primer turno ya están en sus casas y no allí de manera presencial, saber que el ritmo de producción es 24/7 hace que cada una de las personas que forman parte del proceso de alguna forma siga presente y se sienta, a su manera, especial, comentan. “Irse de Toyota es difícil”, resume Lapalma: “Es una empresa muy linda para laburar”.
Otras noticias de Toyota
- 1
Cuánto tendrán que pagar de patente los autos en 2025
- 2
Qué días se roban más autos y cuál es el tipo de vehículo que buscan los delincuentes
- 3
El lanzamiento más esperado del año. Todos los detalles de la Nueva Amarok
- 4
Restauraron un raro e icónico modelo de los ‘60 que perteneció a Niki Lauda y Helmut Marko